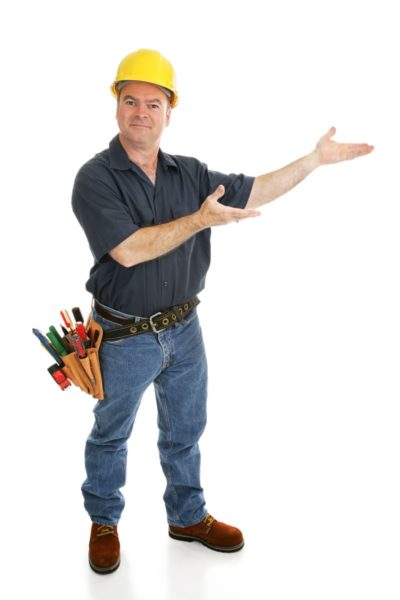
Introdução: O plano de rigging é essencial para garantir a segurança e eficiência em operações de içamento e movimentação de cargas. Neste artigo, exploraremos o que é o plano de rigging, sua importância e como aplicá-lo especificamente em obras de pré-fabricados de concreto.
O que é o Plano de Rigging? O Plano de Rigging consiste em um documento detalhado que abrange todas as fases do processo de içamento, desde a análise das condições do local até a escolha do equipamento adequado, como guindastes. Ele visa minimizar riscos, assegurar a integridade das cargas e das estruturas envolvidas, além de otimizar os recursos disponíveis.
Por que é Importante?
Passos para Implementação:
Análise de Risco:
Seleção de Equipamentos:
Planejamento da Operação:
Treinamento e Supervisão:
Conclusão: O Plano de Rigging é uma ferramenta fundamental para garantir a segurança e o sucesso em obras de pré-fabricados de concreto. Ao aplicá-lo corretamente, você protege sua equipe, sua carga e sua obra.
O bloco de coroamento ou bloco sobre estacas é um elemento estrutural de concreto armado, que é moldado in loco, ou seja, no próprio canteiro de obra. Sua função é transmitir as cargas que chegam na estrutura para as fundações profundas na obra, que são as fundações do tipo estacas ou tubulões.
Os blocos de coroamento são utilizados para distribuir as cargas da estrutura de maneira uniforme para cada estaca ou tubulão na fundação.
No caso de estacas, os blocos podem ser executados sobre diversas estacas e o que vai definir a quantidade delas é a capacidade de carga de cada uma e a resistência do solo, que são fatores muito importantes na escolha do tipo da estaca e do dimensionamento do bloco de coroamento.
No caso de tubulão, o bloco de coroamento é executado sobre um tubulão, se tornando um elemento de transição entre a estrutura e a fundação.
O bloco de coroamento pode ser classificado como bloco rígido ou bloco flexível. Essa classificação é muito importante, pois dependendo do tipo de bloco, o seu comportamento estrutural e método de dimensionamento será diferente.
O bloco rígido, como o próprio nome já sugere, não sofre deformação durante a sua aplicação dentro da obra. Com isso, a rigidez acaba não afetando na transmissão das cargas da estrutura para a fundação.
Dessa maneira, esse tipo de bloco apresenta um comportamento estrutural que possui as seguintes características:
A figura abaixo ilustra como deve ser verificada o valor desse ângulo:
Onde:
Caso o valor do ângulo seja maior que 33,69°, temos um bloco rígido, caso contrário, consideramos o bloco como flexível.
O bloco flexível, ao contrário do bloco rígido, sofre deformação na presença de carregamento chegando da estrutura. Por causa disso, a transmissão das cargas não acontece de maneira uniforme para todas as estacas, o que torna mais complexo definir a distribuição dos esforços para cada uma.
A transmissão varia de acordo com a distância entre o ponto de carregamento no pilar e a estaca. Neste caso, as estacas mais distantes recebem menos carga, quando comparadas com as estacas próximas ao pilar.
Devido a essa complexidade, essa distribuição de cargas nas estacas geralmente é realizada a partir de softwares que utilizam como método de cálculo os elementos finitos.
Com relação ao comportamento estrutural do bloco flexível, a NBR 6118:2014 cita que devemos realizar uma análise mais completa sobre o bloco. Essa análise deve contemplar a distribuição dos esforços nas estacas, dos tirantes de tração e a verificação da punção.
A punção é quando o pilar rompe o bloco por cisalhamento, ou seja, perfurando o bloco.
Para simplificar, imagine um lápis sobre uma folha de papel. Quando aplicamos uma força elevada no lápis, o mesmo acaba perfurando o papel. Isso é o fenômeno da punção.
Por fim, conforme explicamos anteriormente, para que o bloco seja considerado flexível, o ângulo da biela mais afastada deve ser menor que 33,69°.
Assim como o comportamento estrutural, o método de cálculo do dimensionamento é diferente para o bloco rígido e bloco flexível. Por isso, devemos observar com atenção sobre essa classificação, pois a escolha é de grande importância para o melhor desempenho da estrutura.
No caso do bloco rígido com uso de 2 a 6 estacas, utilizamos o método das bielas e tirantes. Inclusive, esse é o método recomendado pela NBR 6118:2014 para o dimensionamento do bloco.
O método tem como base os estudos realizados por Blévot e Fremy, no ano de 1967, que consiste no modelo de treliças internas imaginárias, as quais são submetidas por ações de compressão (bielas) e tração (tirantes).
A figura a seguir apresenta esse modelo das bielas (linhas pontilhadas) e tirantes (linhas contínuas):
Já para bloco rígido com mais de 6 estacas, utilizamos outro tipo de cálculo. O método foi definido pelo Comité Euro-international du Béton (CEB) e Fédération Internationale de la Précontrainte (FIB), em 1970, ou CEB-FIB (1970).
Esse método tem como base a teoria da flexão, em que devemos considerar tensões normais e tangenciais para a verificação da segurança da estrutura.
Até agora, percebemos que todos os métodos são realizados a partir de 2 estacas ou mais, pois o cálculo para 1 estaca é uma situação diferente.
O cálculo é feito a partir dos esforços de fendilhamento, que são esforços de tração transversais em relação à aplicação da carga, os quais o bloco deve evitar.
Com relação ao bloco flexível, não existe um modelo específico para o cálculo do dimensionamento.
Na literatura, existem autores comentando que o cálculo deve ser feito como se o bloco fosse uma sapata flexível, enquanto que para outros, como se fosse uma laje flexível.
O processo de execução de um bloco de coroamento geralmente possui 7 etapas que são:
Na primeira etapa, realiza-se uma abertura da vala que será o bloco de coroamento. É importante salientar que o processo da escavação deve seguir de acordo com as dimensões descritas no projeto de fundação.
Os equipamentos utilizados variam de acordo com o tamanho da estrutura. Para pequenas dimensões, a escavação pode ser realizada de forma manual, e no caso de grandes dimensões, pode-se utilizar equipamentos que realizam esse processo de forma mecanizada.
Por fim, realiza-se o apiloamento do solo, com o objetivo de compactar e regularizar o terreno, e assim, preparando o recebimento do lastro de concreto magro.
Durante a concretagem das fundações profundas (estacas ou tubulões), o concreto é lançado até atingir uma altura maior que a cota de arrasamento.
Isso é feito, pois o concreto que fica no topo das fundações é de baixa qualidade. Sendo assim, nessa etapa, realizamos o corte desse excesso de concreto até a cota de arrasamento.
O nível do topo das fundações não deve ficar no mesmo nível que o solo escavado, mas sim, acima desse nível (geralmente 5 cm acima do nível do fundo do bloco). O motivo é para ajudar na introdução do bloco de coroamento na fundação.
Em relação aos equipamentos, podemos utilizar marteletes ou equipamentos hidráulicos, dependendo do tamanho e da quantidade de fundações existentes na obra.
Além disso, devemos tomar cuidado no momento da preparação pelo motivo de que o corte deve ser adequado, com o topo regular e plano para permitir transferência das cargas conforme previsto no projeto de fundação.
No fundo da vala, coloca-se uma camada fina de lastro de concreto magro (geralmente 5 cm de espessura), que é um tipo de concreto que não apresenta função estrutural.
A sua função é regularizar a superfície do terreno, além de evitar que o bloco de coroamento fique em contato com o solo, pois a umidade e as substâncias químicas presentes no solo podem diminuir a resistência da estrutura.
As formas podem ser feitas de madeira, aço, alumínio ou plástico. Essa montagem é realizada sobre o lastro de concreto magro.
As formas têm objetivo de moldar a estrutura de concreto até atingir a resistência de projeto, além de evitar o desperdício dos materiais presentes no concreto, como os agregados e a água, que são essenciais para o alcance da resistência.
Durante a montagem, é utilizado sarrafo guia e gastalho para guiar no posicionamento das formas do bloco de coroamento.
O travamento vertical pode ser realizado a partir de pontaletes, enquanto que utilizamos vigas ou travamentos metálicos para o travamento horizontal.
E para finalizar essa montagem, utiliza-se tensores de amarração nas formas. Vale lembrar que a montagem das formas deve seguir de acordo com o projeto de fundação, seguindo as dimensões e distâncias calculadas.
Finalizada a etapa da montagem das formas, pode-se iniciar a instalação das armaduras na estrutura, seguindo conforme está descrito no projeto de fundação.
Os cuidados que são necessários ter é com relação ao atendimento das especificações do projeto, ou seja, a quantidade, o tamanho e o espaçamento entre as barras de aço. Ainda, deve-se realizar uma limpeza nas armaduras também.
Isso é feito para que o bloco tire o máximo de desempenho possível, sem causar problemas para a construção.
A instalação das armaduras pode ser realizada fora das formas em caso de blocos de pequenas dimensões. Caso contrário, a montagem deve ser feita dentro das formas, no local indicado no projeto.
Por fim, antes de iniciar a concretagem, é importante fazer uma inspeção na armadura, com o objetivo de observar se está tudo certo em relação ao projeto.
A concretagem é realizada no próprio local da obra, sendo assim, o concreto pode ser preparado no canteiro de obra ou vir pronto das empresas, utilizando o concreto usinado.
Primeiramente, deve-se molhar as formas para que não tenham materiais que se misturem com o concreto, evitando que as formas absorvam a água do concreto, caso o material seja de madeira.
Outro cuidado que temos que observar é com relação ao deslocamento das armaduras durante o lançamento do concreto. Caso isso aconteça, deve-se interromper a concretagem, arrumar as armaduras na posição correta, e só assim, dar continuidade com a execução.
O lançamento do concreto deve ser contínuo para que não exista juntas de concretagem. Deve-se utilizar o vibrador de imersão, com o objetivo de evitar a formação de vazios no bloco. Tudo isso é feito para melhorar o desempenho da estrutura.
A concretagem é finalizada assim que o concreto cobrir toda a armadura e o valor desse cobrimento está presente no projeto de fundação. O cobrimento é importante para evitar que aconteça a corrosão do aço.
A retirada das formas deve ser realizada assim que o concreto atingir sua resistência de projeto.
É necessário tomar alguns cuidados no momento da retirada das formas para que não cause grandes impactos no bloco.
Como a estrutura ficará em contato com o solo, é necessário realizar a impermeabilização do bloco, com o intuito de evitar a infiltração para seu interior.
Finalizada essa etapa, o bloco de coroamento já está pronto para receber o pilar e as cargas que chegam até a estrutura.
No vídeo a seguir é possível visualizar todo o processo de execução de um bloco de coroamento.
Neste artigo, abordamos o conceito do bloco de coroamento, sua classificação e o método de cálculo para cada tipo, além do seu processo de execução. Com isso, esperamos que o texto tenha contribuído para o seu conhecimento acerca do tópico apresentado.
Bloco de Coroamento: o que é, método de cálculo e execução - Escola Engenharia
PEREIRA, Caio. Bloco de Coroamento: o que é, método de cálculo e execução. Escola Engenharia, 2021.
As vigas baldrame são elementos estruturais que têm função de receber cargas da estrutura e transmiti-las aos elementos de fundação.
As vigas baldrame são os elementos estruturais que dividem a infraestrutura (fundação) da supra estrutura (estruturas acima do solo, em geral) e podem ou não estar abaixo do nível do terreno.
Quando falamos apenas em baldrames, há quem conheça como sinônimo de sapata corrida, que é um tipo especial de sapata.
Na concepção estrutural de edifícios em concreto armado, as vigas baldrame recebem as cargas de paredes e outros elementos e as transmitem aos elementos de fundação, como sapatas ou blocos de coroamento.
Quanto ao formato, em nada diferem das demais vigas da edificação, não sendo consideradas parte da fundação em si.
Finalizados os elementos de fundação, como sapatas ou blocos de coroamento de estacas, deve-se dobrar as armaduras e fixar as formas (sustentadas por cimbramento) das vigas baldrame. Dependendo do nível do terreno, pode haver a execução sem o fechamento da face inferior da forma.
A falta desse fechamento pode permitir o escorrimento de nata de cimento, ou ainda uma perda no concreto, comum em concretagem sobre solo. Assim, antes da concretagem, deve-se buscar executar as formas bem rentes ao solo e colocar lastro de brita na superfície inferior.
Após a concretagem das vigas baldrame, com vibração durante a execução e cura nos dias seguintes, deve-se promover a impermeabilização da face superior, a fim de evitar a vinda de umidade do solo por capilaridade à alvenaria da parede imediatamente acima. Essa impermeabilização pode ser feita pela pintura com produtos específicos para esse fim.
As sapatas corridas ou baldrames são elementos de fundação superficial. Elas possuem a função de sapatas, mas diferentemente de outros modelos, não recebem cargas concentradas no centro de gravidade, mas cargas distribuídas linearmente ao longo de seu eixo central. Um exemplo de uso dessas sapatas é na fundação de muros.
Para executar os baldrames ou sapatas corridas, deve-se abrir as valas com a base mais dez centímetros de cada lado. O fundo deve ser apiloado e receber ou um lastro de concreto magro (150 kg/m³ de cimento) ou lastro de brita (compactada, contendo pó-de-pedra).
O passo seguinte na execução está na montagem das formas. A seguir, insere-se a armadura com espaçadores. Há armaduras na base do baldrame (para resistir às tensões de tração, o que diminui o volume concretado em relação ao bloco) ou eventuais armaduras para pilares-parede, quando não falamos de muros.
Por fim, ocorre a concretagem do elemento de fundação. Deve haver vibração adequada para evitar nichos e garantir a resistência mecânica de projeto.
Na era digital, a eficiência e a precisão são
fundamentais em todas as áreas, e a engenharia civil destaca-se como um campo
onde essas qualidades são particularmente valiosas. Diante da complexidade
crescente dos projetos e da imperativa necessidade de otimização de recursos,
as ferramentas que simplificam e potencializam o trabalho dos engenheiros
tornam-se indispensáveis. As planilhas do Excel, disponíveis em nosso site,
representam uma solução robusta e adaptável para uma ampla gama de tarefas na
engenharia civil.
Reconhecendo as dificuldades enfrentadas por alguns
usuários para baixar planilhas e artigos, decidimos oferecer acesso direto a
qualquer material ainda presente em nosso servidor. Este serviço será
providenciado exclusivamente via WhatsApp, e haverá uma taxa simbólica
de R$15,00 para cobrir as despesas operacionais.
Para esclarecimentos adicionais ou em caso de
dúvidas, não hesite em entrar em contato com nosso novo colaborador, João Vitor
do Vale Freitas, pelo e-mail: lojadoclubec@gmail.com. Estamos sempre
prontos para atendê-lo.
Obs.: Em breve planilhas exclusivas.
As fundações rasas apresentam profundidade máxima de três metros e podem ser do tipo: radier, bloco e sapata. Já as profundas apresentam altura superior a três metros e sua base deve ter profundidade superior ao dobro de sua menor dimensão em planta. Podem ser de dois tipos: tubulões e estacas. A diferença entre eles é que na execução do tubulão ocorre descida de operários em alguma etapa, enquanto durante a execução das estacas não ocorre.
Existem variados tipos de estacas e essas podem ultrapassar inclusive o nível de água, ser executadas em campo ou pré-fabricadas e utilizadas em diversas situações: solos coesivos, não coesivos, em alto-mar etc.
Então, quando saber qual tipo de fundação é melhor para cada solo?
A resposta é simples: para que essa escolha seja feita com segurança, é importante analisar as características do solo em que será realizada a construção e fatores como disponibilidade na localidade da obra, custo, prazo, perfil do terreno e proximidade de outras construções.
Para conhecer os tipos de estacas e suas aplicações, continue a leitura.
As estacas podem ser moldadas in loco ou pré-moldadas/de deslocamento. Saiba mais a seguir.
O processo executivo dessas estacas consiste na escavação para posterior enchimento de concreto ou argamassa na perfuração realizada. O solo pode ser retirado ou deslocado durante o processo executivo. Podem ser utilizadas em solos coesivos, não coesivos e com presença de nível d’água, desde que utilizem técnicas de encamisamento.
É uma estaca de base alargada, cuja cravação se dá por meio de golpes sucessivos de um pilão em um tubo que tem a ponta fechada por uma bucha seca de pedra e areia. Quando a cota definida em projeto é atingida, a bucha é expulsa e promove o alargamento da base. A armadura é instalada e, à medida que o revestimento cravado é retirado, o fuste é concretado.
Esse tipo de estaca não deve ser utilizado em terrenos com matacões, construções vizinhas precárias ou terrenos com camadas de argila mole e saturada. Atualmente esse tipo de estaca é pouco utilizado.
É executada por meio da escavação realizada por uma sonda simultaneamente à introdução de um revestimento metálico formado por segmentos rosqueados — até que a profundidade projetada seja alcançada.
A armação é colocada e então, ao mesmo tempo da concretagem, o revestimento é retirado. Não deve ser utilizada em areias submersas, argilas muito moles, saturadas ou quando há presença de lençol freático. É indicada para espaços confinados e apresenta pouca vibração. Entretanto, atualmente é pouco utilizada.
Também denominadas de estacas escavadas, apresentam processo produtivo mais barato e podem ser utilizadas em vários tipos de solos, inclusive com presença de lençol freático, desde que utilizadas camisas metálicas antes da escavação. São executadas por meio de trado helicoidal e posterior preenchimento com concreto.
A perfuração é feita por rotação e sempre que faz-se necessária a retirada de solo, é realizada a subida do trado. Ao atingir a profundidade desejada, posiciona-se a armadura e inicia-se a concretagem da estaca. Quando as camisas metálicas forem reutilizáveis, devem ser retiradas logo após a concretagem.
A estaca hélice contínua consiste na escavação simultânea à concretagem. A escavação é realizada por trado helicoidal contínuo e a concretagem é realizada simultaneamente à retirada do solo.
Essas estacas apresentam ausência de vibração, baixíssimo ruído, variados diâmetros e profundidades de aproximadamente 30 metros, sendo portanto muito utilizadas nos grandes centros urbanos. Após a concretagem, a armadura é colocada. Não podem ser feitas em espaços confinados devido à dimensão dos equipamentos necessários e nem em solos com presença de rochas e matacões.
A estaca ômega é considerada um aprimoramento da hélice contínua. Seu processo executivo consiste na escavação com trado helicoidal sem retirada de solo, uma vez que esse será deslocado e compactado lateralmente.
Também apresenta ausência total de vibrações e atinge profundidades de aproximadamente 30 metros. Quando o trado atinge a profundidade projetada, o concreto é bombeado à medida que esse é retirado e a armadura é inserida.
É uma estaca escavada que pode atingir profundidades superiores a 50 metros e diâmetros que variam de 80 a 500 mm. O processo executivo consiste no encamisamento e perfuração rotativa ou rotopercussiva do fuste, auxiliado por circulação de água.
O solo é retirado e o fuste é estabilizado com lama bentonítica ou polímero sintético. Posteriormente, é retirado o tubo metálico e ocorre o preenchimento com argamassa e colocação da armadura.
A introdução no terreno se dá por meio de processo que não promove a retirada do solo. Essas estacas são constituídas por um ou dois elementos estruturais (madeira, aço, concreto armado ou protendido). Já chegam prontas no canteiro de obras e por isso apresentam maior controle de qualidade. Sua cravação é feita por percussão, prensagem ou vibração.
As estacas pré-moldadas são excelentes opções para solos não coesivos e que apresentam lençol freático próximo ao nível do solo. Além disso, proporcionam economia com bota fora e limpeza da obra, uma vez que não existe escavação.
Contudo, apresentam produtividade inferior às estacas moldadas in loco. Para que seu uso não interfira no custo é importante analisar o valor destinado ao frete, que geralmente é viável quando a fábrica é próxima ao canteiro de obras.
Podem ser de concreto armado ou protendido e apresentar qualquer forma geométrica na seção. A cravação é feita normalmente por meio de percussão, prensagem ou vibração, sendo eficiente o uso de martelos mais pesados com menor altura — evitando danos na estaca durante a cravação.
Não são recomendadas para terrenos com matacões ou pedregulhos, terrenos em que a cota da ponta da estaca seja muito variável, quando as construções vizinhas estão em estado precário ou quando o ruído não é permitido na região.
São estacas formadas por perfis laminados ou soldados, podendo ser simples ou múltiplos. As estacas metálicas devem receber tratamentos para que resistam à corrosão. Podem ser emendadas, mas essas emendas devem resistir ao processo de cravação.
A cravação é feita por percussão, prensagem ou vibração. Entretanto, a cravação por percussão é a mais utilizada, sendo realizada por meio de pilões de queda livre ou automáticos. As estacas metálicas podem ser usadas em muitos tipos de solo, permitem fácil cravação com baixa vibração e apresentam elevada capacidade de carga.
Normalmente, são fabricadas em formatos de seção I, H, circular, quadrada e retangular. Apresentam custo mais elevado do que as demais estacas, mas, mesmo assim, o uso é muitas vezes economicamente viável. São indicadas para solos residuais, que não apresentam profundidade constante e são mais resistentes durante a cravação.
Geralmente empregadas em obras provisórias. Para serem utilizadas em obras permanentes necessitam de proteção contra fungos e bactérias. A cravação geralmente é realizada com martelo de queda livre. Não devem ser utilizadas em terrenos com matacões e quando tiver que penetrar camadas resistentes à ponta, deve ser protegida com ponteira de aço.
Conhecer os tipos de estacas é importante para realizar uma boa escolha quanto à fundação. Contudo, escolher uma empresa confiável é imprescindível para atingir os resultados desejados.
Tenho visto em diversas fabricas e obras, a utilização de carros de mão, conforme figura abaixo, para medir o volume de agregados na confe...