
A produção de concreto em centrais tanto dosadoras quanto misturadoras permite que se obtenha a melhor relação água/cimento no material produzido, alcançando o fator de abatimento (slump) ideal para o traço estabelecido. Essa relação é determinante para a qualidade do concreto estrutural, que também está relacionada a outras etapas do processo, como o transporte, lançamento, adensamento e cura do concreto. No que tange à mistura, todavia, a atuação das usinas de concreto, bem como do caminhão betoneira (no caso das centrais dosadoras), é fundamental para a obtenção do traço programado sem a necessidade de superdimensionar o uso de cimento.
Elton Antonello, gerente de engenharia da Terex, explica que o concreto estrutural deve ser preparado com o mínimo de água possível, mantendo as condições de trabalhabilidade recomendadas para sua aplicação. “A vasta bibliografia existente sobre o tema aponta que quanto mais água é adicionada na fase de mistura, menor será a resistência mecânica do concreto”, diz ele.
Segundo o especialista, isto se deve à segregação dos materiais que compõem a mistura, potencializada quando a quantidade de água presente no concreto é maior durante o seu estado plástico. Isso significa que a segregação ocorre principalmente na fase posterior à mistura, ou seja, quando o concreto é retirado da betoneira. Mas ela também ocorre durante o transporte, lançamento, adensamento e até instantes antes do fim do processo de pega. “Esse fenômeno acontece porque os materiais mais pesados, ou seja, a areia e a brita, tendem a se acomodar no fundo da mistura, enquanto os mais leves, como a água e finos, tendem a migrar para a parte superior do concreto”, ele explica.
Esse deslocamento de materiais torna o concreto poroso, diminuindo sua resistência mecânica. “Por isso, é intuitivo dizer que, quanto mais água existir no concreto, maior será a sua porosidade”, salienta Antonello. Diante dessa avaliação, ele ressalta que o fator água/cimento/porosidade é, indiscutivelmente, o mais importante para o concreto, pois influencia a qualidade tanto da matriz da pasta de cimento quanto da zona de transição entre essa matriz e os agregados graúdos.
Cuidados com a betoneira
Marcelo Antonelli Silva, diretor de equipamentos para concreto da BMC, que distribui a linha da Zoomlion, destaca o impacto desse fenômeno no cotidiano dos profissionais do setor. Ele é enfático ao afirmar que “quem quer controle rígido do traço” precisa ficar atento à retirada da água adicionada ao balão da betoneira após sua utilização. “Sempre que o caminhão retorna à usina, o motorista precisa lavar o balão da betoneira para sua limpeza e parte da água de lastro resultante desse processo permanece no equipamento, prejudicando o traço do concreto que será depositado ali posteriormente”, explica ele.
Quando o assunto são os fatores prejudiciais à qualidade do traço do concreto, aliás, Antonelli cita uma lista que ultrapassa uma centena de itens. No topo do ranking, entretanto, estão as falhas ligadas à eficiência da autobetoneira, a começar pela qualidade das facas de mistura. “Pensando nisso, a Zoomlion desenvolveu a faca dos misturadores de suas betoneiras em formato de T, de modo que o concreto seja sempre puxado para o fundo do balão, potencializando a mistura”, diz ele.
Nos outros modelos disponíveis no mercado, o executivo ressalta que a faca possui revestimentos de vergalhão. “Com o tempo de uso, esse material de desgaste vai se deteriorando e não é incomum encontrar betoneiras circulando com esses revestimentos pela metade.” De acordo com o especialista, isso significa que o concreto não está sendo plenamente misturado durante o transporte.
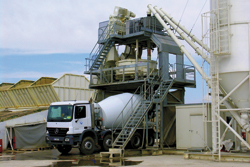
Entre os itens que comprometem a qualidade do traço do concreto, Antonelli também atribui importância ao nível de enchimento do balão da betoneira. Segundo ele, a média dos equipamentos existentes no mercado opera com uma taxa de enchimento de 55% a 59% do espaço total do balão. Isso significa que o espaço interno desses modelos – em geral com capacidade de 7 m³ e 8 m³ – comporta quase o dobro desse volume, mas a parte vazia deve existir justamente para que o tombo do concreto ocorra de forma eficiente dentro da betoneira. “A qualidade do concreto está diretamente relacionada ao respeito ao limite de carga, de acordo com o volume nominal do equipamento”, diz ele.
Outro ponto que merece atenção no transporte com caminhão betoneira é o respeito ao ciclo de movimentação do implemento dentro das especificações necessárias. Geralmente, as betoneiras são programadas para tomar força do motor do caminhão e girar entre 16 rpm e 18 rpm (rotações por minuto). “Aumentar essa velocidade não irá melhorar a mistura do concreto. Pelo contrário, vai piorar e ainda comprometer a viabilidade mecânica do equipamento”, explica Antonelli.
Precisão na pesagem
Para Guilherme Zurita, gerente comercial da divisão de concreto da Liebherr, o motorista do caminhão betoneira também influencia na qualidade do concreto. “Essa influência pode ocorrer não somente em função das rotações programadas para o giro do balão, mas também em função do tempo de viagem até o local de aplicação, o que se agrava em grandes capitais com tráfego intenso”, diz ele.
Zurita avalia que a qualidade do traço também pode ser prejudicada pelo mau funcionamento das usinas dosadoras, pois quanto mais variação apresentar o seu sistema de pesagem, mais longe o traço do concreto ficará daquele idealizado teoricamente.
“Sendo assim, esses itens e mais uma centena deles não citados nesta reportagem influenciam decisivamente na qualidade do traço.”
Para compensar essas eventuais falhas, ele explica que as concreteiras adicionam cimento à mistura em quantidade superior à prevista no traço teórico, o que resulta no maior consumo desse material, que é o item mais caro na produção do concreto.
Zurita explica que uma boa relação água/cimento está vinculada a diversos fatores, começando pela precisão e confiabilidade do sistema de pesagem da usina dosadora e pela medição do nível de umidade da areia.
“A ordem de carregamento dos agregados na betoneira também contribui para a qualidade da mistura, bem como o treinamento dos profissionais envolvidos e o monitoramento constante e detalhado dos corpos de prova, para que reproduzam fielmente em laboratório o estado do concreto aplicado na obra.”
Ele destaca que um corpo de prova moldado erroneamente pode dar a impressão de que todo o concreto aplicado na obra está condenado, obrigando os técnicos da concreteira a adicionar mais cimento ao traço como forma de garantia da resistência final.
0 Comments:
Postar um comentário