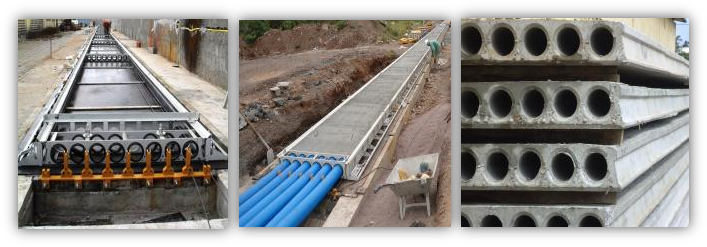
-Racionalização da Obra;
- Redução do Prazo de Execução da Obra;
- Garantia de Qualidade;
- Maior Vida Útil da Obra.
O rendimento de uma equipe de montagem com três operários pode chegar, sem dificuldade, a 50 m²/h, o que equivale a 400m² em oito horas de trabalho.
E quando concluída a montagem dos painéis alveolares, é possível o inicio imediato do preenchimento das juntas, seguindo a equalização e a execução de capa de concreto, sem ter a necessidade de qualquer escoramento dos painéis, em resumo a parte mais demorada e dispendiosa fica por conta do fabricante da estrutura.
Mas, o que é uma laje alveolar?
Segundo a Norma Brasileira, uma laje alveolar é uma peça de concreto produzida industrialmente, fora do local de utilização definitiva, sob-rigorosas condições de controle de qualidade.
Esta laje se caracteriza por uma armadura longitudinal ativa, que engloba totalmente a armadura inferior de tração necessária e por ausência de armadura transversal de cisalhamento.
A seção transversal da laje é alveolar com a presença de almas de concreto e alvéolos formando vazios e deve seguir o que estabelece a Norma Brasileira NBR 12655.
Mas, como se fabrica a laje alveolar?
Existe três formas de se fabricar:
-Em formas
-Em máquinas moldadoras
-Em máquinas Extrusoras
-Em máquinas moldadoras
-Em máquinas Extrusoras
Sendo que produzidas em FÔRMAS as altura usuais são as H12, H16, H20 e H26 com a substituição das laterais e jogos de mangueiras, conforme desenhos dos perfis na imagem que está logo abaixo.
Nesta publicação falarei apenas do processo de fabricação em FÔRMAS.
São dois os processos de fabricação em FÔRMAS:
- Com o uso de imãs para fixar as laterais em pistas MONOLÍTICAS (semelhantes aos da máquinas).
- Com as fôrmas com pista metálica AUTOPORTANTE.
São os seguintes benefícios da pista AUTOPORTANTE:
A forrma Autoportante é utilizada para a fabricação de lajes alveolares com máquinas MOLDADORAS ou EXTRUSORAS ou FÔRMAS com a largura útil de 1,20 ou 1,25m, sendo pré-montada em módulos de 12m + módulo adicional para complementar o comprimento total, composta entre outros com:
Os módulos devem ser concretados com a superfície superior para baixo, com armadura adicional de tela e concreto de 35 Mpa. Após a cura os módulos são desvirados, colocados nos apoios, unidos, nivelados e pós-tensionados. Nos últimos módulos (extremidades), serão montados as cabeceiras (protensão e desprotensão).
Devido ao volume de concreto e a armadura usada os reforços internos e com o pós-tensionamento, a pista torna-se autoportante, e esta pista suporta uma carga de protensão máxima de 350 ton e tm momento máximo admissível de 41 Tf.m
Para garantir a rigidez do conjunto de cabeceiras, durante a protensão e desprotensão, o piso industrial (bloco) onde serão fixadas as cabeceiras, é executado com um volume de concreto de, no mínimo, 14m3 com armadura frouxa.
Nota:
-Para se ter uma carga superior a 350 toneladas, ou mesmo um momento superior a 41Tf.m é necessário se fazer um bloco de fundação como reforço. Este bloco de reforço será definido conforme a carga a ser utilizada e o posicionamento dos aços nas lajes, os quais geram o momento.
-Os Bancos de Ancoragem é uma opção orientativa, pois se necessita estudar o projeto de pista de cada cliente, que é definido em função da concepção da fábrica e disponibilidade de investimento inicial.
Para estudos de viabilidade de implantação da produção, segue abaixo um link para um desenho que ilustra a pista de produção.
Para quaisquer esclarecimentos sobre a aquisição destes equipamentos converse com a Penha Bovo da Weiler e tenho certeza que você será prontamente atendido, a qual agradeço pelas informações enviadas
Eng Ruy Serafim de Teixeira Guerra
Penha Bovo
Gestão de Vendas/Clientes
Weiler C.Holzberger Industrial Ltda
Tel. PABX: (55) 19 3522.5900
Rio Claro-SP-Brasil
Link para o desenho:
3 Comments:
Olha eu gostaria de saber onde posso encontrar essa mangueira azul
Se alguém pode me informar alexsandroigol@gmail.com
Olá, envie seu contato para meu e-mail: vendas01@rubberplastic.com.br falar com GRACE. Obrigada (11) 3906-1019
Postar um comentário